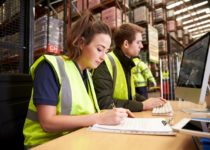
Warehouse operations have a pivotal role to play in the movement of products and overall efficiency of logistics. With better processes in place, as well as optimising features, such as layout and storage, it’s possible to improve the way a warehouse performs. Although there’s no perfect warehouse design, these tips can bring clarity to most setups.
Consider a brand new approach
If you’ve become stuck in something of a rut when it comes to your warehouse processes then a brand new approach could revolutionise the way that you operate, as well as the results that you can achieve. Hiroyuki Hirano, a long-term consultant for Toyota, established the 5S system, which sets out 5 stages for achieving a lean workflow. The stages progress through keeping only what you really need, to creating new standardised procedures. Advantages of incorporating the 5S approach include improving efficiency and quality and reducing cost.
Flow, Accessibility, Space, and Throughput (FAST)
It’s always worth looking at the best practice in your industry to see if the benefits could be applied to your own warehouse management. FAST is a popular and widely used approach that can be useful for improving warehouse design, for example. It has a role to play in optimising physical design, as well as communicating with senior management by attaching KPIs to each of the FAST categories.
Using data to optimise operations
Implementing a Warehouse Management System that collects important operational data – as well as tracking inventory – can provide crucial insight drawn from tracking both fixed and moveable assets. Data that is automatically collected is much more reliable than manually obtained figures and can provide important perspective on how assets are currently treated. For example, you’ll be able to see how inventory moves around the warehouse, identifying the peaks and the lows and making changes to the processes used during those times to improve efficiency.
Set some realistic goals for improvement
Once you’ve gathered data from your own warehouse performance, as well as the best practices that others in the industry rely on, you can start to set realistic goals to measure on an ongoing basis. Defining and tracking an efficient and easy to use returns process, for example, can make a big difference to overall performance, and improving inventory analysis is a key goal for making decisions about where to invest resources to achieve the best warehouse efficiency results.
Reorganise before you expand
It’s always worth pausing before you take a step towards expansion to ensure that you really need the additional space. It may be that more efficient existing operations could create the space you think you need – for example, vertical space is often overlooked as a way to introduce greater capacity and efficiency.
Don’t forget health and safety concerns
It’s very easy to focus on efficiency and results when you’re looking to optimise warehouse management. However, health and safety should never be overlooked. Health and safety issues can be costly for the business and can also impact on performance.
Our warehouse services are optimised for efficiency and performance, with customised reporting procedures and schedules will give you better control over your business and goods. Get in touch with UCS today to find out more.